What is mangrove wood vinegar?
In Matang Mangroves, a hundred years of systematic management and application of silviculture practices have changed the landscape. Most areas are covered by pure stands of the economicallly valuable Bakau Forest (Rhizophora). Bakau make up 85 per cent of the total forest area. These forests are classified as productive forests and are subject to the most stringent of systematic management practices. These forests consist of Rhizophora apiculata and Rhizophora mucronata, the main commercial species.
The history of greenwood, as feedstock of wood vinegar
Careful study is made of greenwood requirements, the efficiency of converting greenwood to charcoal ( which has remained constant from 1980 to 1999), and how long it takes for the conversion to take place. As such, the average burn per kiln for any period can be calculated. For the 2000-2009 periods, the rate was set at 8 burns per year, and greenwood requirement for a single burn at 53 tonnes.
The by-product of converting greenwood to charcoal is wood vinegar. It is collected at the charcoal kilns via a network of long stainless steel tubes and funnel.
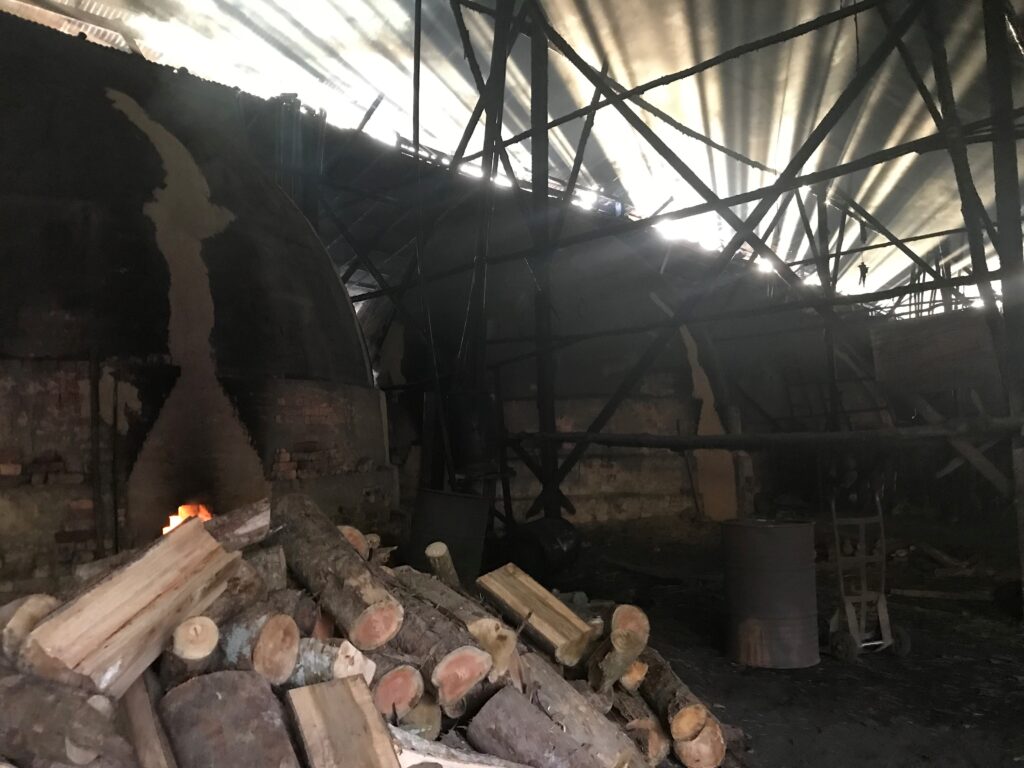
What is Charcoal kiln?
ln the gloom of attap-roofed warehouses, Matang Mangrove charcoal kilns sit in a battery like misplaced giant igloos. However, as charcoal ovens, they (and the processing techniques) have worked so effectively, they have continued to be used with little change since the industry came into being.
The kiln, circa 1930, is popularly called the beehive kiln because of its dome shape. The kiln are constructed of bricks and cemented by a mixture of the clay and sand.

How wood vinegar is produced in Malaysia?
The holes are on the roof of kiln allow steam and gas to escape during firing, and at the side, to provide ventilation for the operators when they empty the kiln after the conversion process. The ideal length of mangrove wood for processing is 1.6m. Logs are cut into billets of these lengths in the field before being sent to the kilns. Prior to being fired, the bark of the logs has to be stripped, since charred bark has no market value. Inside the dome, the billets are arranged vertically, the largest pieces in the center, until they completely fill up the kiln. During the firing, the kiln must be completely sealed. Therefore, the roof vents are closed and the door bricked up except for a small hole which is plugged with clay.
A small connecting tunnel to the kiln is packed with combustible material which is then ignited. Firing in this tunnel continues throughout the burn, which lasts 30 to 35 days. There is no means to regulate the heat, but the burn is estimated to be complete by taking a reading of the temperature, which is taken from the bottom of the door.
Wood vinegar is collected around 12th to 20th day in which temperature of the vapor reaches above 82 degree celsius.
Wood vinegar is send to lab for quality check. The requirement of specifications must be fulfilled.